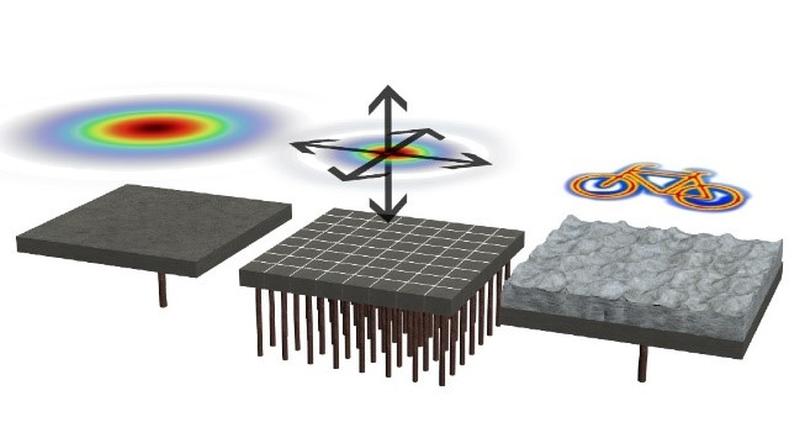
Figure 1.1: Comparison of different sound shaping strategies and achievable degrees of freedom (DOF). Higher DOF leads to more complex sound patterns. From left to right: Single transducer with natural focus (DOF=1), Phased array transducer (as is so far used in medical imaging) with steerable focal point but limited DOF<1000, our simple single transducer with hologram achieves ultrasound images with DOF>10,000.
Introduction and problem: Additive manufacturing, such as 3D printing, opens new avenues for mechanical design, as it allows fabrication of geometries not possible with classical subtractive machining. However, established methods are serial and therefore very slow. Why is it not possible to assemble matter in the desired shape “in one shot”? Ultrasound waves are potentially very interesting, as they are benign and versatile and as they allow contact-free particle manipulation over many length scales. Acoustic waves exert forces when they interact with matter, which has been used to trap and levitate individual microparticles and cells. The acoustic contrast between the material and the medium, and the spatial variation of the ultrasound field determine the interaction. Resonators and arrays of a few hundred transducers have thus far been used to generate the sound fields, but the former only yields highly symmetrical pressure patterns, and the latter cannot be scaled to achieve sufficiently complex fields.
Our approach: A radically new approach to generate ultrasound fields with orders of magnitude higher complexity than what has been possible to date, has been invented in our group [1]. We could demonstrate the first acoustic hologram, which is the acoustic analog to the optical kinoform [1]. This a diffractive element that defines the phase of a passing wave at each point across its wavefront. Theoretically it is now possible to achieve up to 100% diffraction efficiency. The device encodes the desired wave front in the thickness distribution of a plastic slab. Due to the difference in the speed of sound between the hologram and the surrounding medium (e.g. fluid) the passing wave will locally lead or lag at each point depending on the local thickness. The phase distribution that is needed to reconstruct an arbitrary target field can be computed by algorithms, that can be based on established optical holography methods and which we adapted to work for physical acoustics.
Results: We designed and fabricated holograms with an aperture of 50 mm aperture, which effectively contains 15,000 pixels, which is one to two orders of magnitude larger than what has been achieved to date using expensive and cumbersome phased array technology. We showed that commercial printers can be used for the rapid fabrication of the diffractive elements (holograms), which means that they can be easily and cheaply made. We then demonstrated parallel assembly of silicone microparticles into complex shapes defined by the projected acoustic image from the hologram (Fig. 1.2). We expanded this further by a chemical fixation method to allow instant fabrication of objects that can be removed from the bath, while the surrounding bulk liquid remains unaffected [2].
Figure 1.2: Acoustic particle assembly and fabrication. (a) Schematic of the experimental setup (side view). (b) Assembly of microparticles to form a dove (top view). (c) Chemical fusion of the particle assembly results in mechanically stable, self-supporting objects (and potentially much faster than 3D printing).
The large DOF of our holograms enables not only control over the scalar amplitude distribution in the acoustic image. It even allows control over the phase, which is the in-plane component of the wave vector. This can be used for advanced and seemingly dynamic object propulsion techniques, such as the surfing particles shown in Fig. 1.3. There the acoustic image is projected onto the water-air interface where the radiation pressure results in crests on the surface. Rubber discs of several millimeters are trapped on the crests due to surface tension. The hologram can now project elongated tracks with a defined phase distribution such that the trapped particles are continuously propelled around the track as long as the sound stays on.
Creating complex acoustic fields also needs a means to experimentally validate those by measurement. The conventional method works by scanning a hydrophone point-by-point through the region of interest and therefore scales badly to obtain full 3D pressure maps. We therefore also developed a very fast method for mapping 3D sound fields using a thin membrane that is continuously observed by a thermal camera [3]. The evolution of its surface temperature can provide the pressure map of large volumes – orders of magnitude faster than what is possible with a hydrophone.
Figure 1.3: Acoustic propulsion of objects along closed tracks with opposing directions. (a) Schematic of the setup (side view). (b) Photo of the water crests. (c) Simulated phase distribution. (d) Time-lapse image showing motion of discs.
Discussion and Outlook: The advanced control over ultrasound fields – enabled by acoustic holograms – is a major advance for ultrasound research, useful for manifold applications in science, medicine and industry. Holography is a general concept and the algorithms and processes we develop are not limited to static diffractive elements. They can be applied to phased arrays if devices with larger DOF become available. We filed two patent applications on acoustic fabrication and medical therapy, respectively. Parts of this work have been reported as letters to Nature, Advanced Materials, and Applied Physics Letters and received considerable attention in the media and the scientific community. In 2018 this project was awarded two major grants: An ERC Advanced Grant (HoloMan, 2019-2023). We further received a Max Planck - Fraunhofer cooperation grant (Akustogramme, 2018-2022) in collaboration with the Empirical Inference Department at the MPI-IS and the Fraunhofer Institute for Biomedical Engineering.
[P1] Melde, K., A. G. Mark, T. Qiu, and P. Fischer. "Holograms for acoustics." Nature 537 (7621):518-522 (2016)
[P2] Melde, K., E. Choi, Z. Wu, S. Palagi, T. Qiu, and P. Fischer. "Acoustic fabrication via the assembly and fusion of particles." Adv. Mater. 30 (3):1704507 (2018)
[P3] Melde, K., T. Qiu, and P. Fischer. "Fast spatial scanning of 3D ultrasound fields via thermography." Appl. Phys. Lett. 113 (13):133503 (2018)