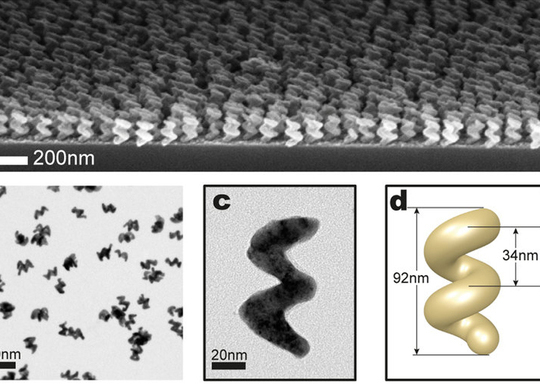
Designing and building nanocomponents to spec
Hybrid, multifunctional nanostructures with diverse 3D shapes and complex material composition can now be manufactured with a precise and efficient fabrication technique
- 13 August 2013
- Micro, Nano, and Molecular Systems
The realisation of nanomachines is inching ever closer to reality. Researchers at the Max Planck Institute for Intelligent Systems in Stuttgart are helping make one of the grand challenges of nanoscience become reality. They have developed a method that makes it possible to manufacture an assortment of unusually shaped and functionalisable nanostructures. It lets them combine materials with widely varying chemical and physical properties at the smallest of scales. The team of scientists headed by Peer Fischer have even grown helical light antennas that are less than 100nm in length from materials which can typically not be shaped at the nanoscale. This is achieved by vapour depositing the material onto a super-cooled rotating disk. Not only does the process allow for the fabrication of nanostructures more exactly than previous methods, several billion of such nanoparticles can be produced in parallel in a rapid manner.
Several of the proposed ideas about what nanotechnology might achieve are rather daring: miniscule robots could transport medications in the human body to foci of diseases or be small enough to operate within a human cell. It could be possible for nanomotors to act as light or toxin sensors at length scales 2.000 times smaller than the thickness of a human hair. Information could be packed into storage devices at densities many times higher than what is achievable with today’s technology. Research into realising some of these goals is already quite close. Now, a team headed by Peer Fischer, Leader of a Research Group at the Max Planck Institute for Intelligent Systems, has come even closer. “We’ve developed a versatile, precise, and efficient process with which three-dimensional nanostructures can be custom fabricated from various materials”, says Peer Fischer. “Up to now, structures less than 100 nanometres could only be created in very symmetrical, primarily spherical or cylindrical shapes.”
With their new method, the researchers are now able to produce hybrid nanoscopic hooks, screws, and zigzag structures by processing materials with very diverse physical properties – metals, semiconductors, magnetic materials, and insulators. As an example of the possible applications, the researchers produced helices of gold that are suitable as nanoantennas for light. The colour of light that the antennas absorb can be controlled by their shape and material composition. With them, circularly polarised light can for instance be filtered, a process used in projectors for 3D movies. Also, the plane of oscillation of an electromagnetic wave – which is what polarized light is - is rotated either clockwise or anticlockwise depending upon the rotational sense of the metal nanohelix. The effect is orders of magnitude larger per helix than what is seen with naturally occurring materials.
Nanostructures from a stream of vapour onto gold nanodot islands
Exact control over the shape and structure of the nanocomponents was achieved by the researchers in Stuttgart by means of their elegant method, which can produce several hundred billion copies of a complex structure in about an hour. With the help of micellar nanolithography, which has been available for several years, they first place billions of regularly arranged nanoparticles of gold onto the surface of a silicon or glass wafer. They deposit gold particles covered in a polymeric shell onto the substrate, which then arrange themselves into a tightly packed, regular pattern. After removing the polymer shell with a plasma, the gold dots remain behind bound to the substrate. The scientists then place the pre-patterned wafer into what is essentially a stream of metallic vapour at an angle oblique enough that the metallic atoms can only see the tiny gold islands and deposit themselves only at those points. Thus, they quickly grow into nanostructures which can have feature sizes as small as 20 nm.
If the researchers slowly rotate the substrate during the during the vapour deposition, the rods wind into a helix. If they rotate the substrate abruptly, a zigzag shape forms. If the material that is being vaporised in the chamber during the process is changed, a composite material, such as a metal alloy, is formed. And of course, all of these neat tricks can be combined. For example, they attached copper hooks to aluminium oxide rods using a thin layer of titanium to adhere the two materials together.
The crucial idea: liquid nitrogen cooling
“Larger structures have been produced for a while already in a similar fashion”, explains Andrew G. Mark, a Max Planck researcher who played an important role in developing the method. “Up to now, this method could not be transferred to nanostructures, however.” This is because the hot, mobile atoms deposited from the vapour rapidly arrange themselves on the surface into a sphere due to energy considerations. “We therefore came up with the idea of cooling the substrate using liquid nitrogen at about minus 200 degrees Celsius, which flows through the substrate holder, so that an atom is quickly frozen and fixed into position as soon as it lands on the apex of the growing nanobody”, says John G. Gibbs, who likewise contributed significantly to the work at the Max Planck Institute for Intelligent Systems.
Despite the versatility of the method, not all shapes can be created with it. “Because the structure always grows away from the wafer, no rings, closed triangles or squares can form”, says Fischer. “We are not able to build a nanoscale Eifel Tower.” Nevertheless, wide-ranging opportunities are open to him and his team. “Our long-term goal is to construct nanomachinery”, says Peer Fischer. “Nature builds motors on the scale of about 20 nanometres. We would like to couple our components to these motors.” Then it may be possible for many of the nanoreseachers’ dreams to become a reality.
People
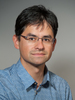